…Guyana banks on modern asphalt plant
…citizens to cash in with sale of recyclable materials
GUYANA is months away from being home to the most modern asphalt plant in the Caribbean Region, which will enable it to build roads at a better quality, while utilising recyclable materials like plastic and rubber.
The modern plant is expected to be completed by September and is already being hailed as the equipment designed to meet Guyana’s post 2020 road infrastructure goals. It will also provide a source of income to Guyanese wishing to turn in their plastic containers or old tyres for their use in road building.
On Tuesday, Minister of Public Infrastructure, David Patterson; Demerara Harbour Bridge Corporation (DHBC) General Manager, Rawlston Adams, and Permanent Secretary at the ministry, Kenneth Jordan, visited Demerara Shipping Wharf for a follow up inspection of some of the equipment which arrived. Guyana’s current asphalt plant has a major issue whereby it does not meet the country’s standard for dust emissions. Many complaints have been received as a result but to fix this would be very costly.
Proving a solution to the issues altogether, the new 27 meters high asphalt plant will have zero dust emission and can produce approximately 160 tons of asphalt per hour which is four times faster than the current asphalt plant.
Minister Patterson told the media that when the present government took over in 2015, it started the process of improving the existing asphalting infrastructure through the use of a mobile asphalt plant. While additional materials were acquired in 2016, the Ministry realised that the amount of road works needed in Guyana far outweigh the capabilities of the current facilities.
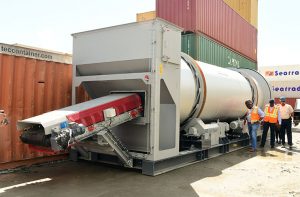
“It quickly became very apparent that the volume of work that we were doing countrywide, we had outlived our usual supply. Even though it’s adequate [and] it’s working now, we could do much better,” Patterson said.
As such, since 2017 efforts have been geared towards acquiring a new asphalt plant which would revolutionise the quality of roads in Guyana. “When established, [the asphalt plant] will be the biggest for the country,” Patterson said. “We can actually do more work at a cheaper cost.”
In explaining why the plant is being referred to as ‘modern’, Adams revealed that it was built in Germany this year with added specifications requested by the government of Guyana.
For example, the plant’s dryer drum, where all the raw material enters for a drying process, has intentionally been made thicker than the one now utilised in the current plant which will prevent wear and tear.
Asked how the average Guyanese will benefit from the plant, Adams stated: “They will benefit from better quality roads. We will now be able to produce a lot of asphalt because the demand for infrastructure development post 2020 is going to be very, very high. In [almost] every community the problem is roads so we’re now saying ‘we have the capacity to produce asphalt of the highest quality that will suffice those demands’.”
The DHBC General Manager estimates that by early 2020, personnel will be trained in mix designs to incorporate rubber and plastic which can be used along with bitumen thereby creating a new industry for many Guyanese to profit from. “The car tyres that are being thrown away you can take that, chip it and use that as part of the materials. This is why we’re saying this plant is a modern plant and it is the most modern plant that you will find in the Caribbean,” Adams began.
“People will no longer be throwing away their plastic containers; somebody will be there picking it up, cleaning it, chipping it and they’ll be able to come and sell it to us once we have those things in place.”
A total of 34 pieces of equipment will make up the plant and most of it is galvanised to cater for the high moister area at the Garden of Eden where the operation will take place.
A careful tendering process is ongoing to finalise a contractor for the building of the plant’s foundation while the company from which the asphalt plant was purchased is responsible for installation.
“The intention is for us to have all the engineers who will be working on this plant be part of the installation process so that they will be au fait and aware of all the components and how it fits together. So, it’s not that the supplier will come and work independently and they’ll come and set up this plant and go, part of the requirement is training,” the DHBC General Manager explained.
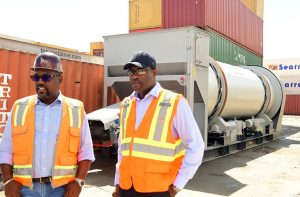
The total installation period will take six weeks while, after the first six months of operation, local operators will be sent to Germany for further training. If operators in Guyana encounter a challenge with the plant, they can contact the supplier in Germany who can easily diagnose and adjust the electronic settings of the plant through the internet.
The computerised system calculates the right type, texture and size of materials needed for construction and this enables contractors to know and maintain a consistent level in the quality of road being built. The government has several ongoing road projects which will run into 2020 and several more planned as Guyana seeks to improve its infrastructure countrywide.